1. 传统质量控制为何频繁“失灵”?
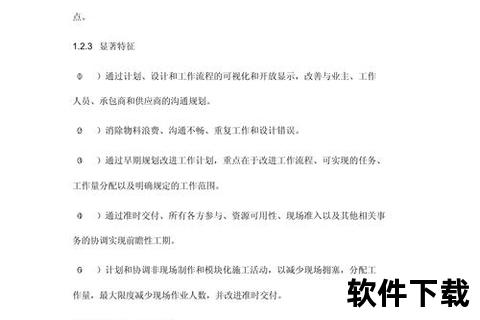
某汽车零部件供应商曾因0.3毫米的尺寸偏差导致整批次产品报废,直接损失超600万元。传统质量管理模式下,工人每2小时抽检5件产品,但问题发现时已生产了2万件。这种滞后性在制造业普遍存在——美国质量协会2023年数据显示,采用人工抽检的企业平均质量问题发现周期为6.7小时,而缺陷产品流入下道工序的概率高达32%。
智能革新SPC软件的出现改变了这种被动局面。在浙江某精密铸造企业的实践中,部署实时监测系统后,通过136个传感器每秒采集27项工艺参数,将质量异常发现时间缩短至8秒内。系统自动触发设备停机指令,使缺陷产品数量从月均153件降至4件,仅三个月就收回改造成本。这种将事后检验转变为过程控制的技术革新,正是智能革新SPC软件引领高效精准品质管控新浪潮的核心价值。
2. 实时监控是“纸上谈兵”吗?
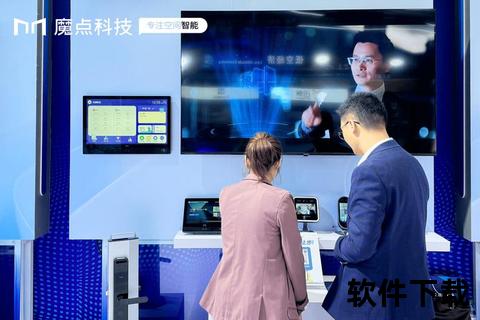
东莞某电子连接器制造商的案例极具说服力。该企业过去依赖工程师手动分析质量报表,新产品良品率提升周期长达45天。引入智能SPC系统后,通过机器学习建立的工艺参数优化模型,将试产阶段的缺陷类型识别速度提升17倍。系统自动生成的38种DOE(实验设计)方案,帮助企业在12天内就将良品率从68%提升至93%。
更值得关注的是动态预警功能的应用。当某批次原材料的硬度值出现0.5%的波动时,系统立即调整冲压设备的压力参数,避免了可能产生的500万元损失。这种实时响应的能力,使得企业首次实现"缺陷预防率"达到89%的突破,充分印证智能革新SPC软件引领高效精准品质管控新浪潮的实际效能。
3. 数据分析只能依赖人工经验?
在山东某轴承制造企业的质量中心,资深工程师王工曾需要3天时间分析200组检测数据。现在,智能SPC系统不仅能自动生成包含17个质量维度的诊断报告,还能通过历史数据模拟预测未来8小时的生产质量趋势。在2023年8月的实际应用中,系统提前36小时预警了热处理工序的炉温漂移趋势,避免了可能发生的批量性硬度不合格问题。
更令人惊讶的是跨工序关联分析能力。某食品包装企业发现,当注塑机温度波动0.5℃时,后续印刷工序的套准精度会下降15%。这种隐藏在数百万条数据中的关联规律,被智能系统在23秒内识别出来。通过建立98个参数间的数学关系模型,企业实现了整体质量成本的27%降幅,生动演绎着智能革新SPC软件引领高效精准品质管控新浪潮的数据魅力。
对于计划进行智能化改造的企业,建议分三步实施:首先建立关键质量特性(CTQ)的数字孪生模型,其次选择支持边缘计算的硬件架构,最后构建渐进式的算法训练机制。初期可重点监测前三位质量缺陷源,逐步扩展到全流程管控。要注意保留至少6个月的历史数据用于模型训练,并与设备维护系统实现数据互通。选择软件时,建议要求供应商提供至少3个同行业成功案例,并实测系统在20000数据点/秒场景下的处理能力。