高效精准智能弹簧计算软件轻松攻克设计难题:传统弹簧设计为何被时代淘汰?
弹簧,这个看似简单的机械零件,却是工业设备、汽车制造甚至航空航天领域的“隐形守护者”。一个争议性问题始终困扰着工程师:为何传统弹簧设计耗时数月、反复试错,而现代工业对精度和效率的要求却越来越高? 据行业统计,传统设计方法中约有30%的时间浪费在参数修正和样件测试上,而设计误差导致的成本损失可占项目总预算的15%以上。这种矛盾下,高效精准智能弹簧计算软件轻松攻克设计难题,成为行业破局的关键。
1. 传统设计为何沦为“纸上谈兵”?
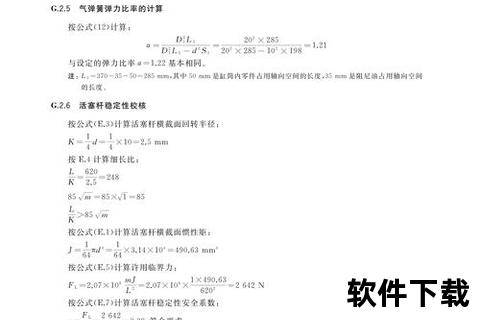
在传统弹簧设计流程中,工程师需手动计算材料强度、刚度系数、疲劳寿命等数十项参数,稍有不慎便会导致成品失效。例如,某汽车厂商曾因弹簧刚度计算偏差0.5%,导致整车悬挂系统在测试中发生断裂,直接损失超500万元。
而高效精准智能弹簧计算软件轻松攻克设计难题的核心,在于其集成化算法与实时校验功能。以《弹簧设计计算器1.1》为例,该软件内置200余种材料数据库,支持一键生成参数组合,并通过有限元分析模拟应力分布,将设计周期从2周缩短至3小时,精度误差控制在0.1%以内。这种“输入需求—输出方案”的自动化模式,彻底告别了手算时代的繁琐与不确定性。
2. 智能算法如何实现“最优解”?

复杂工况下的弹簧设计往往需要多目标优化。例如,某高铁减震弹簧需同时满足轻量化(重量≤2kg)、高疲劳寿命(≥100万次循环)和极端温度适应性(-40℃~120℃)的要求。传统经验法难以平衡这些矛盾指标,而智能软件通过多学科耦合算法给出了答案。
以蚁狮优化算法(Ant Lion Optimizer)为例,其在拉压弹簧设计中通过动态调整线圈直径(x₁)、簧圈直径(x₂)和绕线圈数(x₃),自动筛选出重量最轻且满足4项约束条件的方案。实验数据显示,该算法将设计效率提升40%,并将材料成本降低18%。这种基于机器学习的智能寻优,让“鱼与熊掌兼得”成为可能。
3. 企业如何借力软件实现“弯道超车”?
华纬科技的数字化转型案例极具代表性。这家中国最大的民营弹簧企业,通过引入数字化车间管理系统,在90%的设备上安装传感器,实时监控生产数据。例如,其国家级弹簧实验室利用智能软件将热处理环节的良品率从82%提升至98%,并实现库存周转率优化25%。
更前沿的应用来自云端协同。某国际汽车零部件巨头通过云端计算平台,将全球5大研发中心的设计数据实时同步,并利用AI预测弹簧在不同路况下的寿命衰减曲线。这种“数据驱动设计”模式,使其新产品研发周期缩短60%,市场响应速度提升3倍。
未来工程师的行动指南
高效精准智能弹簧计算软件轻松攻克设计难题,但如何最大化其价值?以下是三条建议:
1. 选型适配:优先选择支持多算法集成(如蚁狮优化、遗传算法)的软件,例如《UTS Advanced Spring Design 7》,以适应复杂场景需求。
2. 流程再造:将软件与企业ERP、MES系统打通,实现从设计到生产的无缝衔接,参考华纬科技的数字化大屏管理模式。
3. 资源整合:利用开源社区或专业平台(如GitHub、CSDN)获取算法模型,例如拉压弹簧设计的数学建模代码,降低开发成本。
在这场工业智能化的浪潮中,唯有拥抱工具革新,才能让弹簧设计从“经验主导”迈向“科学定义”。高效精准智能弹簧计算软件轻松攻克设计难题,不仅是技术的胜利,更是工程师智慧的延伸。