一、DFM软件只是“查错工具”?它如何重构设计与制造的对话桥梁?
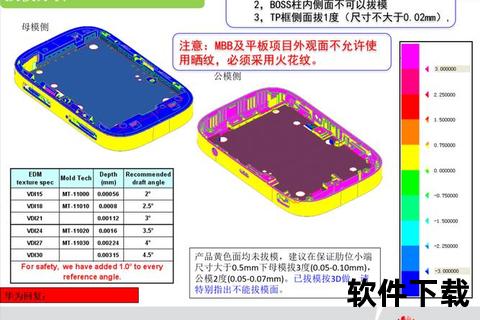
当某手机品牌新品因PCB散热设计缺陷导致百万台产品召回时,人们发现:设计工程师引以为傲的0.1mm精密走线,在批量生产时却成为贴片机无法识别的工艺灾难。这样的故事在电子行业反复上演——2023年工信部数据显示,我国电子信息制造业因设计制造脱节导致的返工损失高达127亿元,相当于每天烧掉3480万元。
传统研发模式中,设计师与工艺师如同隔着玻璃墙对话。华秋电子调研显示,30%的工程师从未进行可制造性分析,DFA(可装配性设计)功能使用率更低于10%。这种割裂直接导致:设计师的创意结晶在产线上变成“工艺不可能三角”——既要性能卓越,又要成本低廉,还要快速量产。
典型案例:特斯拉Model 3通过DFM优化,将底盘零件从70个压铸为1个整体结构,不仅实现车身减重15%,更使产线效率提升40%。这印证了行业共识:80%的制造成本在设计阶段锁定,60%的工艺问题源自架构设计初期。
二、智能时代,DFM如何实现“设计即制造”的魔法蜕变?
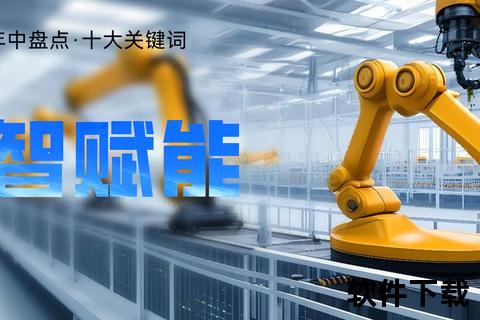
当传统Checklist升级为智能决策引擎,DFM软件正在演绎三重进化论:
1. 全流程数字孪生:某汽车电子企业引入参数化DFM系统后,成功将BMS控制板的开发周期从12周压缩至5周。系统自动比对300+工艺参数,提前规避32类潜在失效模式,使首件良率从68%跃升至95%。
2. AI驱动设计优化:华秋DFM的机器学习模型,通过分析500万+元器件数据库,可在30秒内生成最优元件布局方案。其9月份拦截的问题数据显示,62%的可装配性缺陷通过AI预测提前规避。
3. 云端协同生态:国内某无人机厂商使用云端DFM平台后,实现跨6省9厂的设计工艺同步。平台自动匹配不同工厂的设备能力差异,使新产品转移效率提升300%。
三、DFM+工业互联网=?智能制造生态如何破局成长痛?
当某智能穿戴企业遭遇“十万级订单交付危机”时,DFM软件给出的解决方案令人惊艳:
通过工艺仿真模块,提前验证12种柔性电路板折叠方案
对接MES系统生成动态工单,使换线时间从2小时降至15分钟
整合供应链数据,自动匹配替代物料应对芯片短缺危机
这种变革背后是生态级进化:全球最大压铸机厂商IDRA的Giga Press系统,通过与DFM软件深度集成,使模具开发周期缩短60%。设备参数直接反哺设计系统,形成“设计-制造-优化”的智能闭环。
更值得关注的是知识沉淀革命:某军工电子企业将三十年工艺经验转化为8000+条智能规则,使新工程师的设计达标率从43%飙升至89%。这种企业级工艺DNA的数字化传承,正在改写“老师傅退休即技术断层”的行业困局。
构建智能制造的三大行动指南
1. 分阶段引入智能DFM工具:从基础规则检查(如华秋DFM免费版)起步,逐步扩展至云平台+AI模块,避免一次性投入过大
2. 建立跨部门DFM联席会议:参照丰田“大部屋”模式,每周组织设计、工艺、采购三方协同会议,用数据说话而非经验争论
3. 投资工艺仿真实验室:头部企业应将年度研发预算的15%-20%投向数字孪生系统,特别是5G+工业互联网融合应用场景
当DFM软件革新性驱动智能制造的高效引擎,卓越生产体验已不再是愿景。数据显示,全面应用智能DFM的企业,其新品上市速度提升40%,质量成本下降58%,这正是智造时代给予创新者的超额回报。在这场没有终点的进化赛中,把握住DFM这把金钥匙的企业,终将在智能制造的新纪元中铸造属于自己的“工业诗篇”。