一、传统工业控制为何难以满足智能化需求?
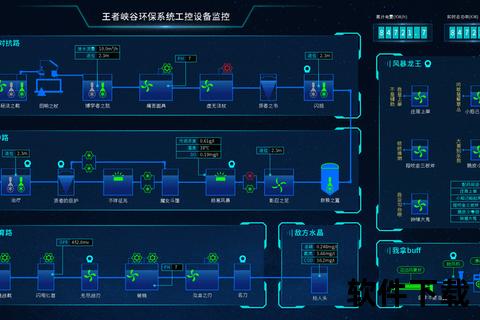
在制造业转型升级的浪潮中,一个争议性问题浮出水面:传统工业控制技术是否已成为智能制造的瓶颈?根据国际机器人联合会(IFR)的数据,2024年全球工业自动化市场规模突破4000亿美元,但仍有60%的企业面临设备兼容性差、控制精度不足等问题。在这一背景下,台达PLC编程软件凭借其“高效掌控智能未来:台达PLC编程软件赋能精准工业控制”的核心理念,正在重塑工业控制的新格局。
以某汽车零部件工厂为例,其原有PLC系统因逻辑复杂、调试周期长,导致生产线停机率高达15%。而引入台达ISPSoft软件后,通过模块化编程和实时数据示波器功能,仅用3周便完成程序优化,设备综合效率(OEE)提升22%。这印证了智能化控制工具对传统工业痛点的突破价值。
二、台达PLC软件如何实现“一键式”效率跃升?
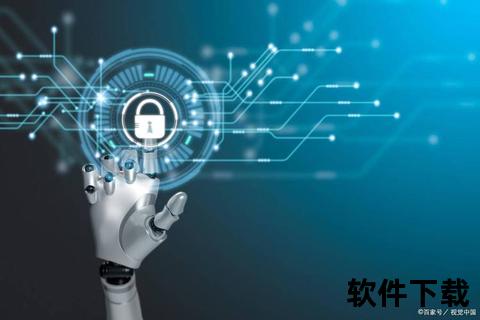
1. 编程语言:从“手工劳作”到“智能协同”
台达PLC支持梯形图(LD)、结构化文本(ST)、顺序功能图(SFC)等5种编程语言,其中结构化文本在处理复杂算法时效率提升50%。例如,在深圳某3C电子厂,工程师使用ST语言开发视觉检测程序,将图像分析指令执行速度从200ms缩短至80ms,良品检出准确率提升至99.7%。
2. 硬件联动:打破数据孤岛的秘密武器
通过ISPSoft软件的硬件规划功能,台达PLC可同时连接伺服驱动器、HMI人机界面和智能传感器。青岛某智能仓储项目中,工程师仅用1天便完成128个IO点的配置,并通过EtherCAT总线实现0.1ms级同步控制,物流分拣速度提升3倍。
3. 仿真调试:让试错成本归零
WPLSoft V2.46的模拟运行功能,使浙江某注塑机制造商在无实体设备情况下,提前发现3处逻辑冲突,避免价值200万元的生产事故。数据显示,该功能可将调试周期压缩40%,故障率降低65%。
三、精准控制如何破解工业场景的“不可能三角”?
案例1:新能源电池生产的微米级挑战
宁德某锂电池企业要求极片涂布厚度误差≤2μm。台达DVP-EX2系列PLC通过14位高精度模拟量模块,结合PID闭环控制算法,将涂布均匀度标准差控制在0.8μm以内,材料损耗减少18%。
案例2:柔性制造系统的动态重构
东莞某家电企业采用台达AS系列PLC搭建柔性生产线,通过SFC编程实现12种产品型号的快速切换。借助运动控制功能库,机械手定位精度达到±0.02mm,换型时间从45分钟缩短至8分钟。
案例3:跨地域设备的云端协同
在跨国食品集团的项目中,台达PLC通过DCISoft软件构建工业物联网,实现中德两地5家工厂的设备状态同步。异常响应时间从6小时降至15分钟,年节省运维成本超500万元。
四、从“能用”到“善用”的进阶指南
高效掌控智能未来:台达PLC编程软件赋能精准工业控制的关键,在于构建“工具+人才+数据”的铁三角:
1. 工具选择:针对中小型项目推荐WPLSoft(易学易用),复杂系统首选ISPSoft(支持IEC 61131-3标准);
2. 能力培养:参考《台达PLC编程技术及应用案例》中的122个实战模板,重点掌握定时器嵌套、数据块加密等核心技术;
3. 数据驱动:利用数据示波器功能记录关键参数,建立设备健康度评估模型,例如通过振动频率预测轴承寿命,准确率可达85%。
当前,全球工业4.0进程已进入深水区。台达PLC编程软件以“高效掌控智能未来:台达PLC编程软件赋能精准工业控制”为锚点,正在书写中国智造的新篇章——这不仅是一场技术革命,更是一次从“经验驱动”到“算法驱动”的认知跃迁。对于企业而言,抓住这个转型窗口期,就意味着掌握了智能制造时代的入场券。