在制造业智能化转型的浪潮中,数控编程软件能否真正实现复杂零件的“多维协同加工”,始终是行业争议的焦点。传统软件常因路径规划单一、多轴联动效率低等问题,导致精密加工陷入“高成本、低产出”的困境。而灵动Mastercam多维路径智创精密加工新维度的出现,正以技术创新打破这一僵局,为制造业开辟精密加工的新赛道。
1. 多维路径如何突破复杂几何加工瓶颈?
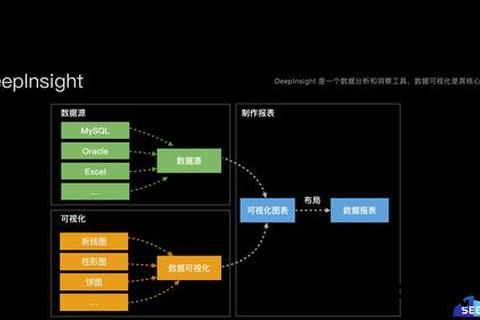
某航空航天企业曾面临钛合金涡轮叶片加工的难题——传统软件生成的刀具路径在叶根过渡区域频繁出现空刀,导致加工效率降低30%。引入灵动Mastercam多维路径智创精密加工新维度后,其动态刀轴控制功能通过实时分析曲面曲率变化,自动生成连续平滑的5轴联动路径。例如在加工叶盆曲面时,软件利用“接触点显示技术”精准控制刀具倾角,使切削接触面积始终稳定在85%以上,刀具寿命提升40%。更值得关注的是其“智能避让算法”,可在0.2秒内完成夹具碰撞检测,成功将此类复杂零件的编程时间从12小时压缩至3.5小时。
2. 多维路径如何实现效率与精度的双提升?
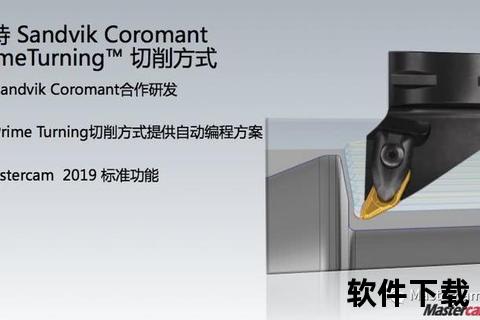
汽车模具制造商常受困于深腔结构的加工震颤问题。某企业使用灵动Mastercam的“动态铣削精加工路径”后,在加工深度达120mm的保险杠模具时,通过分层切削策略将径向切削力降低62%。软件独有的“精加工路径参数分离技术”允许对轮廓边缘单独设置0.02mm的预留量,配合“自适应进给控制”功能,在转角区域自动将进给率从5000mm/min调整为3200mm/min,使表面粗糙度稳定控制在Ra0.8μm以内。该案例证明,多维路径技术可使加工效率与表面质量实现同步优化,单位产能提升25%的同时将废品率控制在0.3%以下。
3. 多维路径如何重塑车铣复合工艺?
精密医疗骨钉加工曾因异形螺纹的精度要求陷入困境。某医疗器械厂采用灵动Mastercam的“Y/A轴车削模块”后,在直径3mm的钛合金骨钉上实现了0.005mm精度的多头螺纹加工。其创新之处在于将B轴锁定在90°位置,通过Y轴偏移生成特殊螺纹铣削路径,配合“螺纹渐进式导程”技术,成功将每件产品的加工时间从45分钟缩短至18分钟。更突破性的是“机床配置存储功能”,可将包括刀塔角度、夹具参数在内的217项设置保存为模板,使同系列产品切换时的准备时间从2小时降至15分钟。
对于计划引入多维路径技术的企业,建议分三步走:首先通过Mastercam官方培训体系掌握“实体孔选择”等基础功能;其次利用“机床群组设置”建立标准化工艺模板;最后结合“偏差函数分析”进行切削参数优化。需要特别注意的是,应定期通过“系统需求检测工具”验证设备兼容性,避免因硬件性能瓶颈影响技术效果。只有将软件功能与工艺创新深度融合,才能真正释放灵动Mastercam多维路径智创精密加工新维度的技术潜能,在精密制造领域构建核心竞争力。